Introduction to Construction Site Safety
Construction sites can be hazardous environments. Implementing safety measures is crucial to prevent injuries and accidents. As the site manager, it is my duty to prioritize worker safety through proper planning, training, and adherence to regulations. This includes ensuring adequate lighting and tool hire.
Proper illumination helps workers navigate the site, identify hazards, read plans, and perform tasks safely. Renting equipment from reputable suppliers provides access to well-maintained tools that meet quality and safety standards. By addressing these factors upfront in my safety plan, I can dramatically improve site conditions for everyone.
The Role of Lighting in Construction Safety
Construction sites contain many trip and fall hazards. They also use potentially dangerous equipment and involve work at odd hours or in enclosed spaces. Adequate lighting is essential for workers to perform duties safely. It helps them see obstacles, read warning labels, avoid electrical hazards, and more.
I always conduct a thorough assessment of lighting needs across all construction phases. Factors like the type of work being conducted, time of day, and weather conditions inform suitable temporary or permanent lighting solutions. As the project progresses, lighting plans must adapt to evolving requirements in different zones.
Overview of Essential Construction Tools
Construction crews use a wide variety of motorized and hand tools daily. Common electrical tools include circular saws, drills, angle grinders, and more. My crews also rely heavily on hand tools like hammers, wrenches, screwdrivers, and shovels.
These tools boost productivity but also pose risks like electrocution, cuts, crushing injuries, sparks, and noise. My responsibility is properly maintaining and safely operating tools to mitigate hazards. I also ensure the right tools are used for each task per manufacturer guidelines.
Assessing Lighting Needs for Different Construction Phases
Construction lighting needs to change dramatically across projects. A foundation crew working inside a commercial excavation requires different lighting than roofers finishing exterior work. I break the project into phases and zones and then evaluate each one separately.
Key factors in my assessments include type of work, weather, time of day, worker positions, natural light availability, indoor vs outdoor zones, openness of space, temporary structures blocking light, and more. This allows me to optimize lighting specifically for the unique needs of each phase.
Key Considerations in Selecting Construction Lighting
Choosing suitable temporary or permanent lighting involves evaluating many options and features. Key factors I consider include:
- Lumens – total brightness of light
- Light color – cool, neutral, or warm options
- CRI – color rendering accuracy
- Power source – battery or electric
- Durability – resilience for outdoor use
- Adjustability – movable light direction
- Ease of installation – quick setup
- Operating costs – energy efficiency
I select cost-effective lighting tailored to each zone’s demands. Durability and adjustability provide flexibility as conditions evolve.
The Impact of Poor Lighting on Worker Safety
Insufficient or inconsistent site lighting significantly raises safety risks. Low visibility of hazards, blocked emergency exits, deep shadows, and eye strain provoke accidents.
Specific dangers include:
- Tripping on debris/tools
- Misjudging distances
- Electrical shocks
- Using tools unsafely
- Failure to see warning signs
- Limited hazard visibility
- Glare blindness
- Muscle fatigue from squinting
These predictable risks are unacceptable. My lighting choices aim to mitigate them through consistent, directed illumination adapted to each construction zone.
Best Practices for Construction Site Illumination
I adhere to best practice guidelines for illumination planning:
- Provide general area lighting for overall visibility
- Include task lighting for specialized work zones
- Choose impact-resistant fixtures
- Use diffusers to reduce glare
- Provide adequate emergency lighting
- Have mobile light sources like flashlights
- Ensure lighting remains effective as site changes
- Provide a minimum of 50 lux across access routes
- Mark guy wires on tall structures
- Avoid directing lights into worker’s eyes
- Keep lighting consistent with area work types
- Inspect and clean lights regularly
Following these standards tailored to each zone optimizes safety through stellar visibility.
Integrating Tool Hire into Your Safety Plan
My responsibilities don’t end once I purchase or rent tools. I must manage equipment effectively across its lifecycle through:
- Initial inspection on receipt
- Testing before first use
- Ensuring operators are trained
- Tracking tool locations
- Ongoing inspection/maintenance
- Proper tool storage
- Preventative repairs
- Decommissioning damaged tools
I integrate these practices into my planning from the outset when choosing rental suppliers. This allows me to compare vendors on maintenance track records and safety standards upfront.
Evaluating Tool Rental Companies for Quality and Reliability
Tool hire companies vary enormously in quality. I rigorously assess suppliers against key benchmarks:
Safety
- Regular inspection/testing
- Tagging damaged tools
- Preventative maintenance programs
- Worker training on tools
- Certified electrical safety
- Incident reporting procedures
Inventory
- Sufficient tools in good repair
- Tools meet regulatory standards
- Diversity of equipment options
- Rapid replacement of damaged items
Service
- Flexible rental terms
- Transparent pricing
- Delivery logistics options
- Excellent customer service reputation
- Inventory tracking systems
This due diligence ensures my rented tools are safe, compliant, and suited to my needs. Streamlined arrangements with reputable vendors make site management simpler.
Benefits of LED Lighting in Construction Environments
I actively favor LED lighting solutions due to major advantages:
- 80% more efficient than incandescent bulbs
- 50,000+ hour lifetime per bulb
- Highly durable for outdoor use
- Operate well in cold temperatures
- No glass components are prone to breaking
- Instant start-up and re-starting
- Excellent light color quality
LEDs also offer adjustable brightness, directionality, and superior cold tolerance. These features support tailored, cost-effective lighting across every construction application.
How Proper Lighting Enhances Productivity and Safety
Quality lighting is an investment, not a cost. Well-lit spaces help workers avoid strain or fatigue while sharply boosting productivity and accuracy.
Benefits include:
- Increased tool/task visibility
- Identifying errors quickly
- Avoiding redundant work
- Easier collaboration between teams
- Finding dropped items faster
- Reading plans and signs effortlessly
- Security cameras capturing clearer footage
- Boosting motivation and morale
I observe 30-50% productivity gains in my well-lit zones. This efficiency compounds safety by reducing fatigue-related accidents.
Checklist for Safe and Effective Construction Lighting
My construction lighting checklist ensures adequate visibility for every task and hazard:
General Area
- Minimum 50 lux across access routes
- Consistent light across a full zone
- No dark corners or shadows
- Lighting suits weather conditions
- Directions minimize glare
Task Lighting
- Fixed/portable options available
- Task zones supplemented 50+ lux
- Match light color temperature to use
- Easily adjustable angles/brightness
- Emergency backup lights if fixed fails
Outdoor Lighting
- IP65 or higher ingress protection
- Mounting suits environmental factors
- Point down to reduce light pollution
- Mark guy wires on tall structures
Electrical
- Use LED bulbs for efficiency/safety
- Prevent water collecting on wires/fixtures
- Safety cut-offs if power disrupted
- Lightning protection if relevant
This checklist evolves across zones and phases but always promotes excellent illumination.
The Role of Personal Protective Equipment (PPE) in Lighting Safety
Beyond fixed lighting, personal protective equipment (PPE) provides movable illumination. Hard hats can integrate adjustable LED spotlights to target visibility. Some models include rear lamps to alert others.
For tasks in extremely dark zones, I mandate workers wear dedicated headlamps. These battery-powered LED lights connect directly to helmets for hands-free operation. Headlamps improve visibility without compromising mobility.
I incorporate suitable headlamps/hard hats into my PPE requirements for laborers working in insufficient ambient lighting conditions. This supplementary personal lighting remains vital even with my best fixed lighting efforts.
Navigating the Challenges of Outdoor Construction Lighting
Outdoor operations pose unique lighting challenges, including:
- Exposure to elements like rain or wind
- Running wiring across long distances
- Limiting disturbance to the local area
- Directing lighting only on site
- Light pollution regulations
- Power access with generators
- Preventing vandalism/damage
I mitigate these factors by using durable, energy-efficient LED lights on mobile equipment and vehicles throughout outdoor zones. These wirelessly-charged battery lamps provide targeted illumination. I supplement them with inflatable lighting towers offering powerful area lighting movable to shifting work zones.
Case Studies: Successful Lighting Strategies in Construction
Examining case studies provides tangible examples of effective construction lighting strategies:
The Seattle Rain Tunnel
The Seattle Rain Tunnel revised lighting mid-project once crews began underground work. The dark, cramped environment caused strained visibility and injuries. Switching to LED headlamps with rear straps prevented shadows during tasks. Hard hat spotlights also assisted communicating across the 35-foot diameter tunnel. These simple, affordable changes dramatically improved working conditions.
Safeco Field
Retractable roof installation at Safeco Field ballpark utilized powerful metal halide floodlights suspended from cranes. As phases progressed, engineers repositioned the lights using hoists to match the active roof sections. This dynamic, responsive positioning optimized visibility and accuracy when aligning huge trusses overhead.
These cases demonstrate the power of adaptable, phase-specific lighting. Even simple affordable tweaks can enhance site safety significantly.
Understanding the Costs of Lighting and Tool Rental
Budgeting adequately for quality lighting and tools ensures availability and safety. tant expenses include:
Lighting
- Purchase price ranges from $50 for headlamps to $2,500+ for light towers
- Transformer, wiring, and control costs for fixed installations
- Electrician fees if installing custom systems
- Energy consumption from extended use
Tool Rental
- Daily/weekly rates often >10% equipment value
- Transportation fees if relevant
- Insurance costs for higher risk tools
- Late return penalties
- Cleaning fees if returned dirty
Carefully estimating long-term costs for my chosen equipment allows me to assess affordability and optimize value. This lightens unexpected budget impacts down the road.
Safety Guidelines for Using Electrical Tools on Site
Power tools underpin construction but pose serious risks if misused. My electrical safety protocols minimize hazards:
- Inspect cords/tools for damage pre-use
- Ensure circuits have sufficient capacity
- Use residual current devices and isolation switches
- Don’t carry tools by cords
- Store safely to prevent crushing cords
- Prevent water/liquid contact with power tools
- Use tools within operating temperatures
- Prohibit freehand operation whenever possible
- Ensure operators wear full PPE
- Secure workpieces with clamps when possible
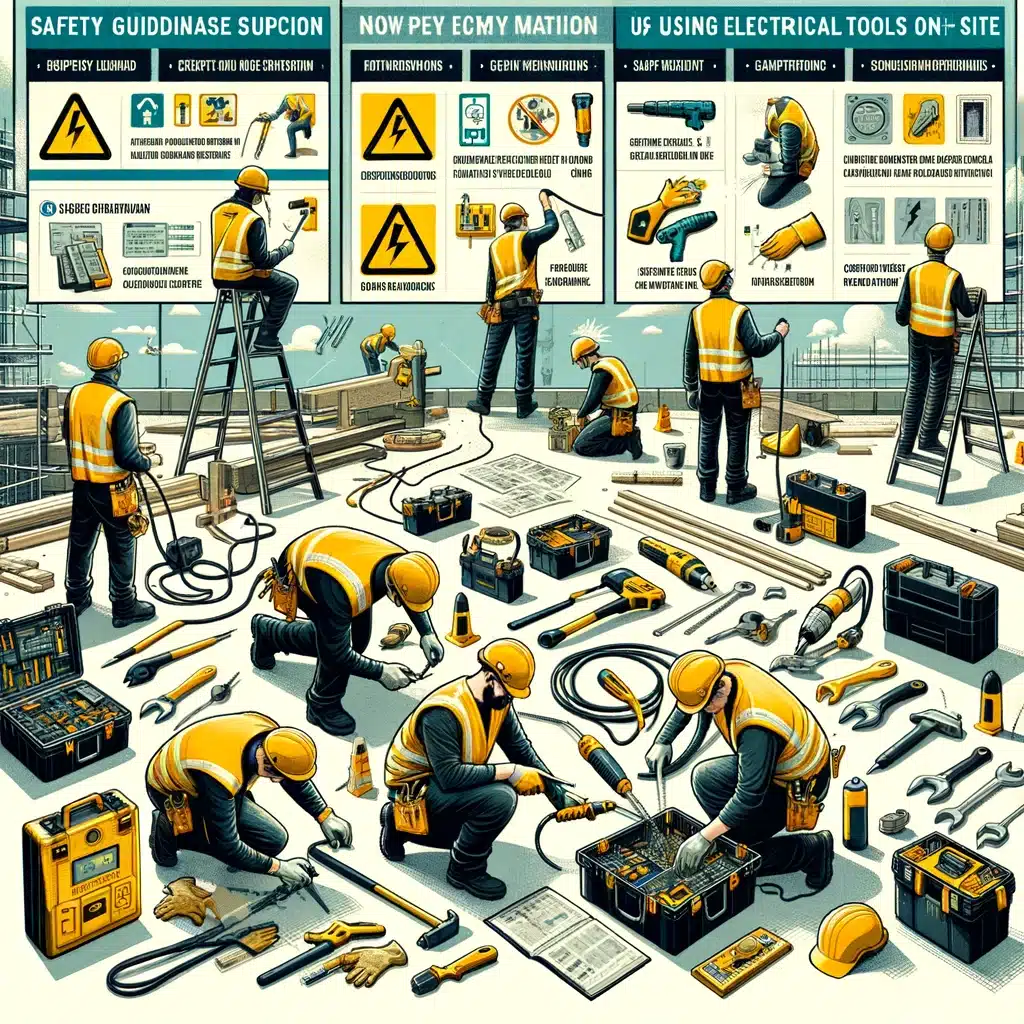
I enforce tight compliance since electrocution accidents still occur too frequently on work sites. Safety training and supervision ensure tools are only used properly.
Maintenance Tips for Construction Lighting Equipment
Diligent equipment maintenance is crucial for lighting reliability and longevity. I follow key guidelines:
Routine Inspections
- Check wiring integrity and connections
- Clean air vents on lighting units
- Assess lamp alignment/aiming
- Ensure mounting hardware remains secure
- Spot check representative light samples for failures
Ongoing Maintenance
- Wipe bulbs and fixtures to increase light output
- Lubricate light tower mast cranks
- Re-coat light pole foundations to prevent rust
- Replace faulty bulbs immediately
Storage
- Fully retract mast on light towers
- Store indoor lamps in cool, dry locations
- Cover fixtures when not in use
- Clean dust and dirt from lamps/lenses
These simple procedures sustain optimal illumination despite harsh site conditions.
The Interplay Between Natural and Artificial Construction Lighting
Balancing natural and artificial light achieves the best overall site illumination. I coordinate these strategies:
- Angle fixtures to supplement, not compete with the sun
- Shift outdoor task timing based on light availability
- Close window shades in rooms with temporary lights
- Turn off indoor lamps near exterior openings
- Attach translucent panels on dark enclosures
- Use light sensors to automatically adjust brightness
- Provide shade from glare when working east/west
This integration creates uniform light coverage while conserving energy. It also sustains visibility when weather blocks sunlight unexpectedly.
Emergency Lighting: Preparing for Power Outages
Despite precautions, blackouts periodically occur on sites. Emergency lighting provisions maintain basic visibility:
Fixed Lighting
- Install battery backup systems on key circuits
- Designate and illuminate emergency exits
- Distribute independent emergency lamps
Personal Lighting
- Mandate backup headlamp use when power is unstable
- Store backup headlamp batteries onsite
- Provide portable emergency lanterns
I ensure emergency lighting meets minimum regulatory levels across access routes and exits. This enables safe evacuation and prevents panic during outages.
Training Workers on Safe Lighting and Tool Use
Classroom training provides foundational knowledge, but hands-on supervision cements those learnings about lighting procedures and tool operation. My training regimen includes:
- Classroom – Review equipment instructions, discuss recent incidents, cover new protocols
- Individual – Provide 1:1 instruction adjusting/operating equipment per worker’s needs
- On-site – Shadow workers using tools, and correcting techniques in real-time
- Certification – Require passing safety/skills verification before independent operation
- Refresher – Annual re-training revisits fundamentals after incidents
This layered development approach tailored to various learning styles gives me confidence every worker knows protocols. I document all training which also protects me legally.
Energy Efficiency and Sustainability in Construction Lighting
Construction exerts massive environmental impacts from energy and resource consumption. My site lighting choices aim to conserve:
Efficiency
- Use LED technology broadly
- Take advantage of renewable solar power
- Use timers and light sensors to reduce waste
- Specify EnergyStar-certified fixtures
Control Light Pollution
- Direct lights downward to prevent skyglow
- Install shields around bare bulbs
- Reduce lighting when the site inactive
Sustainable Materials
- Favor renewable, recyclable materials
- Responsibly dispose of lamps like LEDs containing arsenic
These efforts reduce costs while shrinking the overall footprint of my lighting designs. This attention to sustainability also appeals to environmentally-conscious clients.
Legal Requirements for Construction Site Lighting
Local regulations impose legal obligations for minimum lighting levels to protect public and worker safety. Common standards include:
- Mandatory illumination along access routes
- Minimum fixed lighting on stairs
- Backup emergency lighting systems
- Construction phase-specific directionality
- Timed security lighting activation
- Rules limiting offsite glare/light pollution
- Protection near helicopter landing pads
- Warning illumination on tall/isolated structures
I consult current ordinances when designing site lighting plans. This ensures legal compliance from the earliest phases to avoid enforcement actions down the line.
Innovations in Construction Lighting Technology
Exciting lighting innovations unlock smarter, more sustainable designs:
- Tunable LEDs adjust color temperature
- Lighting controls enable remote monitoring/operation
- BLE sensors integrate lighting with other systems
- Flexible OLEDs enable curved light fixtures
- Solar-powered off-grid area lighting
- Natural light sensors balance artificial/sunlight
I actively pilot new technologies like these to enhance efficiency. Features like automation, integration, and tunability provide lighting-on-demand for crews across every conceivable scenario.
The Risks of Inadequate Lighting in Construction Zones
The consequences of poor construction lighting span from nuisance to life-threatening:
Minor
- Difficulty reading plans/instructions
- Eye strain headaches for workers
- Tools/materials lost in shadows
Moderate
- Glare-related temporary blindness
- Increased workplace stress
- Elevated long-term vision issues
Major
- Moving vehicles striking workers
- Using machinery unsafely
- Working from heights risks
- Electric shock & burns
I treat minor lighting issues seriously since small factors quickly compound into major incidents if neglected site-wide.
Choosing the Right Tools for Specific Construction Tasks
Standardizing tools for crews prevents using incorrect or unsafe equipment incorrectly. I match tools to uses including:
Concrete Work
- Concrete mixer – blending aggregates
- Floats – smoothing flatwork finish
- Shovels – distributing concrete
Framing
- Circular saw – cutting boards/studs
- Reciprocating saw–notching framing
- Hammer drill – driving lag bolts
Excavation
- Excavator – digging trenches
- Jackhammers – breaking concrete/rock
- Plate compactor – preparing subgrades
This basic alignment ensures I rent specialized tools where necessary while avoiding unnecessary costs. Workers can complete tasks safely and efficiently with purpose-built gear.
Balancing Cost and Quality in Tool Hire
Tool rentals represent a major project expense. Yet purchasing certain equipment outright makes no financial sense for one-off jobs. I strike a balance using these guidelines:
- Rent infrequently used tools like scaffolding
- Rent when short construction phase timeframes
- Rent highly specialized tools operators lack the expertise to use
- Consider rent-to-own agreements on major equipment to capture residual value
- Purchase commonly used tools like circular saws, drills
- Purchase cheaper hand tools not require complex maintenance
- Purchase laser levels, and safety gear – used daily across projects
Tool management software helps me assess utilization rates and true costs specific to my workflows. This drives data-backed decisions on renting vs buying optimized to my budgets.
Careful evaluation of precisely which tools merit purchase or rental best serves productivity and the bottom line simultaneously.
Environmental Considerations in Construction Lighting
Construction lighting carries environmental side effects from raw materials extraction, electricity generation, and improper lamp disposal. I mitigate impacts through:
- Choosing LED bulbs containing no mercury
- Seeking lighting made from recyclable aluminum
- Responsibly disposing of lamps to avoid soil contamination
- Prioritizing renewable solar power charging batteries
- Programming lighting sensors to conserve off-hour electricity
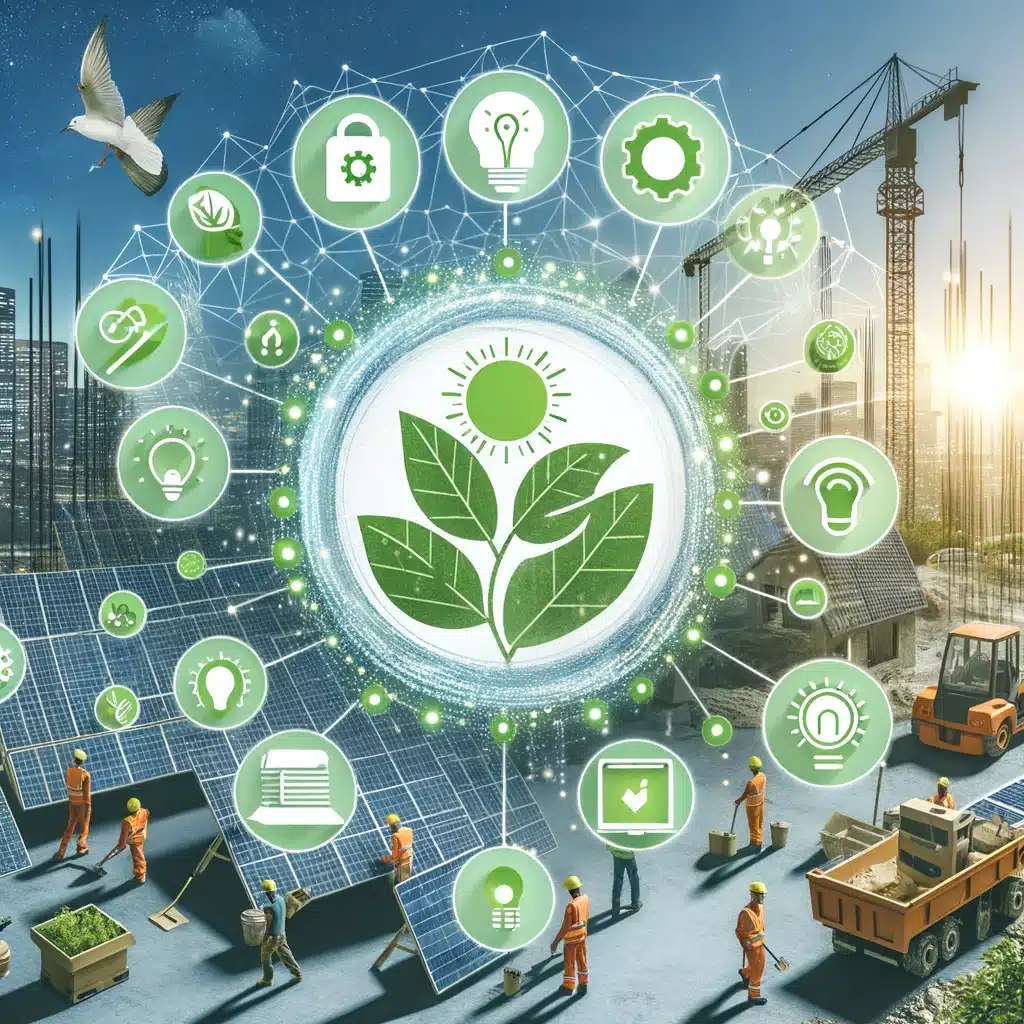
I also calculate projected carbon emissions from extended use during design. This motivates reductions enhancing project sustainability. Simple changes make a substantial difference.
Lighting Solutions for Specialized Construction Projects
Unique building projects present distinct lighting obstacles. Consider these examples:
Underground: Confined spaces like tunnels mandate lighting meeting combustibility standards while handling humidity. I install wirelessly networked magnetic LEDs on tunnel roofs for flexibility.
Waterfront: Maritime projects like piers tackle corrosion. My customizable LED tower clusters feature marine-grade waterproof connectors suitable for ocean spray conditions.
Historic Renovations: Sensitive restoration demands avoiding damage to delicate finishes from heavy fixtures. Low-heat LED spotlights with tiny profiles installed along preservation zones prevent harm.
Every construction light scenario presents singular difficulties. Responsive custom solutions targeting specific challenges best satisfy specialized needs while preventing safety issues.
Future Trends in Construction Lighting and Equipment Rental
Rapidly advancing technology will enhance future construction site lighting and equipment availability:
Connected Lighting
- Remote monitoring/diagnostics of light fixtures
- Centralized lighting control optimization
- Automated responses to ambient conditions
AR/VR Tools
- Immersive training simulations
- Hazard visualization overlays
- Remote expert collaboration
Autonomous Vehicles
- Self-driving material delivery
- Automated surveillance/monitoring
- Robotic inspections for quality/safety
These innovations will profoundly expand what is possible across my sites concerning responsive real-time lighting, accelerated skill development, and prevention of dangerous scenarios before they arise.
Building a Culture of Safety: Lighting and Tools
Instilling a zero-injury mindset in workers requires consistent modeling of safe behaviors from management plus open communication. Tactics I use to promote safe lighting and tool usage include:
- Reward safety innovation ideas
- Praise proper PPE compliance
- Publicize incident stats at meetings
- Empower crews to report issues quickly
- Address concerns transparently and quickly
- Lead by example wearing PPE properly myself
- Discipline unsafe operations strictly
I aim for a trust-based culture focused on collective responsibility for safety outcomes. The wellbeing of individual workers matters more than any deadline. Teams embracing this during lighting and tool operations keep project risk contained.
Addressing Common Misconceptions About Construction Lighting
Many question construction site lighting expenditures given competing budget priorities. However, flawed assumptions undermine safety and productivity. I correct frequent misconceptions including:
“Daytime lighting is unnecessary”
Changing weather rapidly alters visibility, including sudden storms. All access routes require minimum fixed illumination regardless of the hour.
“Just use vehicle headlights at night”
Headlamps fail to provide area lighting for hazards like trip risks and don’t align with active task zones. Dedicated wide-beam standalone lighting remains essential across dusk-to-dawn shifts.
“Use cheaper incandescent bulbs”
Although less expensive upfront, incandescent bulbs burn out faster, provide less brightness per watt, emit more heat, and break easily compared to LEDs. Higher quality LEDs pay back their premium rapidly through energy savings and avoided replacements.
Addressing these myths has convinced numerous clients of lighting upgrades their crews ultimately appreciated immensely via performance benefits and prevented close calls.
Conclusion: Enhancing Safety Through Strategic Lighting and Tool Hire Choices
Construction leaders must pursue worker wellbeing vigilantly across every site activity. Overlooking factors as basic as lighting and tools multiply risk exponentially.
Meanwhile, optimized illumination and equipment access afford profoundly positive impacts reaching far beyond safety. Efficiency and sustainability also improve through deliberate choices fitted to exact site requirements.
I implement a lifecycle perspective to manage risks, seeking dynamic solutions adaptable as site conditions evolve hour-to-hour. Precision visibility paired with purpose-built gear offers the clearest path to maximizing productivity while preventing avoidable incidents.
Through advancing technology and consistent training, I ensure lighting and tools promote rather than endanger our essential human work building the structures supporting society daily. Our lives literally depend on this commitment.